浙江镁铝合金压铸工厂
随着铝合金材料的普遍应用,铝合金压铸技术逐渐崭露头角。铝合金以其轻质、高的强、耐腐蚀等特性,在电子、汽车、电机、家电和通讯等行业得到了普遍的应用。铝合金压铸技术凭借其高精度、高效率的特点,成为这些行业不可或缺的生产工艺。铝合金压铸技术具有许多卓著的优势。首先,压铸工艺可以实现高精度的零件生产,满足行业对零件尺寸和形状的高要求。其次,压铸生产效率高,能够在短时间内生产出大量的零件,满足大规模生产的需求。此外,铝合金压铸件具有良好的表面质量和机械性能,能够满足各种复杂环境下的使用要求。铝合金压铸工艺,细节决定成败。浙江镁铝合金压铸工厂
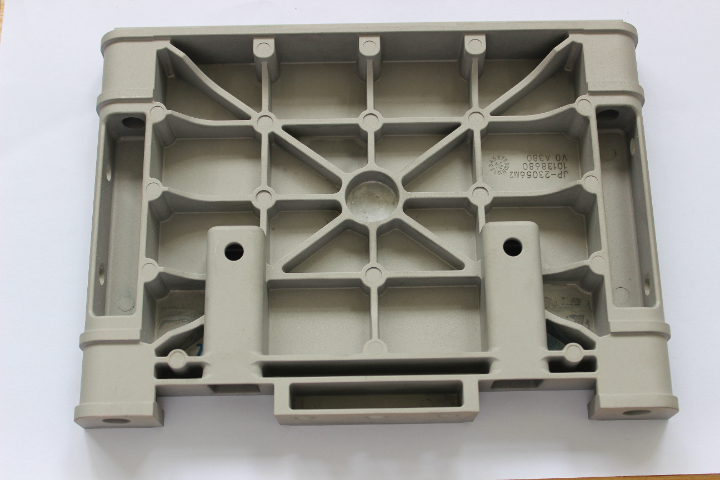
在压铸技术的发展过程中,斯图吉斯的设计起到了关键作用。他设计并制造了首台手动活塞式热室压铸机。这台机器的出现,使得压铸技术得以更加高效、精确地应用于工业生产中。随后,默根瑟勒对压铸技术进行了深入研究,发明了印字压铸机,进一步推动了压铸技术的发展。进入19世纪60年代,锌合金压铸零件的生产开始兴起。这一时期的压铸技术主要应用于小型零件的生产,如钟表零件、玩具零件等。虽然这些零件的体积较小,但要求精度极高,因此压铸技术得以迅速发展。同时,锌合金压铸零件的出现也为后来的铝合金压铸技术提供了借鉴和参考。浙江镁铝合金压铸工厂高压压铸技术,铝合金品质提升。
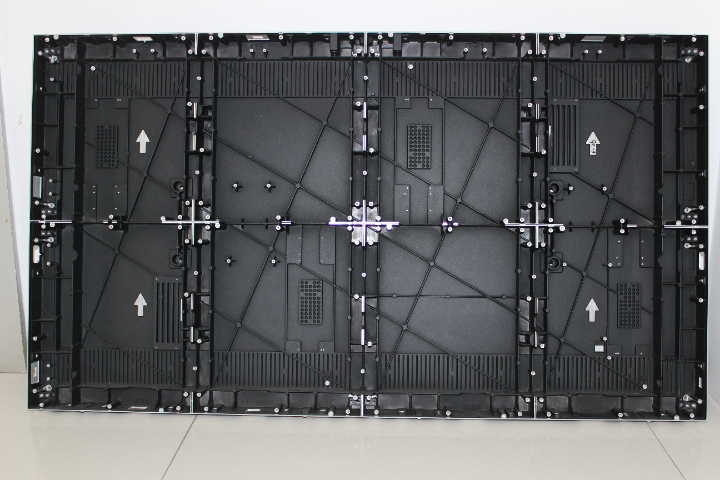
铝合金压铸件的质量检测是确保产品合格的重要环节。在压铸完成后,需要对铸件进行尺寸测量、外观检查、力学性能测试等多项检测。这些检测能够及时发现铸件中的缺陷和问题,确保产品符合标准和客户要求。同时,质量检测还能够为压铸工艺的优化提供数据支持,帮助企业不断提高产品质量和生产效率。铝合金压铸在汽车工业中的应用尤为普遍。汽车发动机缸体、缸盖、变速器壳体等关键部件都采用了铝合金压铸技术。这些部件不只要求具有高的强度和耐磨性,还需要具备轻量化的特点以降低整车油耗。铝合金压铸技术能够满足这些要求,为汽车工业的发展做出了重要贡献。
在铝合金压铸技术的实际应用中,需要注意一些关键因素。首先,选择合适的铝合金材料是保证压铸件性能的基础。不同的铝合金材料具有不同的性能和用途,需要根据具体的应用场景进行选择。其次,设计合理的模具结构是保证压铸件精度和质量的关键。模具的结构设计需要考虑零件的形状、尺寸、精度等因素,以确保压铸件能够满足设计要求。此外,控制压铸过程中的温度和压力也是保证压铸件质量的重要因素。铝材磷化技术是铝合金压铸过程中的重要环节。磷化处理可以提高铝合金表面的耐腐蚀性和耐磨性,改善其表面性能。在铝材磷化过程中,选择合适的磷化剂和促进剂是关键。硝酸胍作为一种有效的促进剂,可以提高磷化速度和质量。同时,氟化物、Mn2+、Ni2+等添加剂也可以改善磷化膜的性能。通过调整磷化液的成分和工艺参数,可以获得性能优良的磷化膜层。铝合金压铸件,轻量化优先选择材料。

铝合金压铸技术的发展历程中,威廉姆·乔奇和斯图吉斯等先驱者的贡献不可忽视。他们通过不断的实验和探索,为铝合金压铸技术的发展奠定了基础。其中,斯图吉斯设计并制造了首台手动活塞式热室压铸机,这一创新性的设计为后续的铝合金压铸技术发展提供了重要的技术支撑。在铝合金压铸技术的发展过程中,促进剂的研究和应用起到了关键作用。硝酸胍作为一种有效的促进剂,因其水溶性好、用量低、快速成膜的特点而被普遍应用。硝酸胍的加入可以卓著提高铝合金压铸产品的质量和性能,为铝合金压铸技术的普遍应用提供了有力保障。精密压铸,铝合金零件完美呈现。四川笔记本支架铝合金压铸厂家
压铸铝合金,提升产品竞争力。浙江镁铝合金压铸工厂
铝合金压铸技术的中心在于模具设计和材料选择。模具设计需要充分考虑产品的形状、尺寸和精度要求,以及铝合金的流动性和凝固特性。材料选择则需要根据产品的使用环境和性能要求,选择合适的铝合金材料和添加剂。这些都需要经过专业的技术团队进行深入研究和实践。在铝合金压铸过程中,温度控制是非常关键的一环。温度过高或过低都会影响铝合金的流动性和凝固特性,从而影响产品的质量。因此,需要采用先进的温度控制系统,确保整个压铸过程中温度的稳定性和均匀性。浙江镁铝合金压铸工厂
惠州市臻鑫精密技术有限公司是一家有着先进的发展理念,先进的管理经验,在发展过程中不断完善自己,要求自己,不断创新,时刻准备着迎接更多挑战的活力公司,在广东省等地区的五金、工具中汇聚了大量的人脉以及**,在业界也收获了很多良好的评价,这些都源自于自身的努力和大家共同进步的结果,这些评价对我们而言是比较好的前进动力,也促使我们在以后的道路上保持奋发图强、一往无前的进取创新精神,努力把公司发展战略推向一个新高度,在全体员工共同努力之下,全力拼搏将共同惠州市臻鑫精密技术供应和您一起携手走向更好的未来,创造更有价值的产品,我们将以更好的状态,更认真的态度,更饱满的精力去创造,去拼搏,去努力,让我们一起更好更快的成长!
上一篇: 浙江常用铝合金压铸件厂家
下一篇: 河北无人机配件压铸件结构